下穴の公差
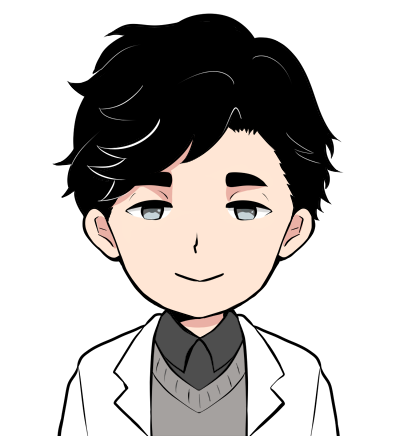
SugarBox
実は下穴径には公差が存在しているんだ。
今回は公差を表示するために省略版の下穴表を拡張するよ!
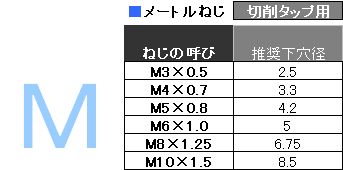
まず、目安として下穴を調べる際に
タップ – ピッチ = 下穴径 という計算式が存在しています。
例)タップM6 – ピッチ1.0 = 下穴径5.0
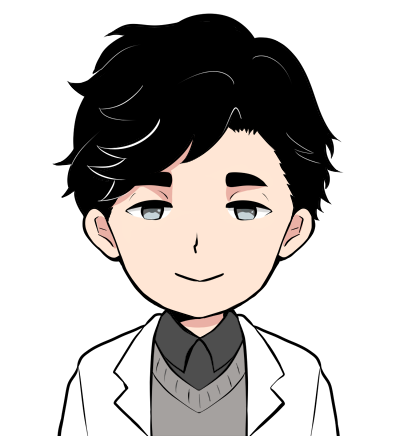
SugarBox
例外はあるけど一般的なネジなら
この計算でなんとかなることが多いよ!
下穴表の公差を表示して拡張すると次のようになります。

推奨下穴径の穴を目標値に
最小下穴径〜最大下穴径の間におさめます。
求められているねじの等級にあった最大下穴径を選択します。
例)等級4Hの場合、M3×0.5 推奨下穴径 2.5(公差幅 2.46~2.54)
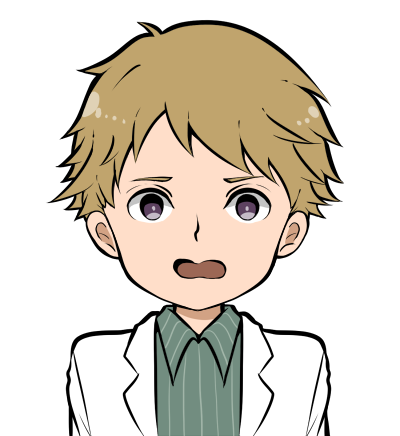
新入社員
等級って調べたんですが、
よくわかならいですよ!?
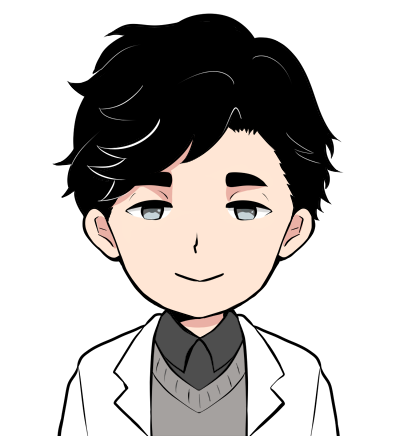
SugarBox
等級がよくわからない場合は
最大下穴径部分の各最小値を
超えていないなら特に気にしなくていいよ。
ひっかかり率
なぜ下穴径を管理するのかというとひっかかり率が関係します。
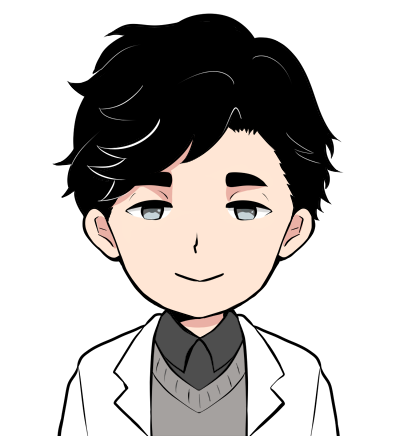
SugarBox
おねじとめねじの接触部分の比率についての話だよ。
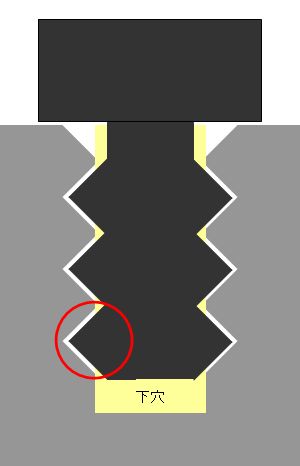
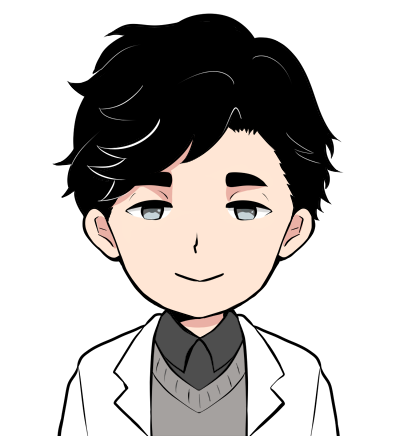
SugarBox
下穴径が小さいと、ひっかかり率は大きくなるよ。
加工の際に負荷が増えるからタップが折れやすくなるよ。
加工の際に負荷が増えるからタップが折れやすくなるよ。
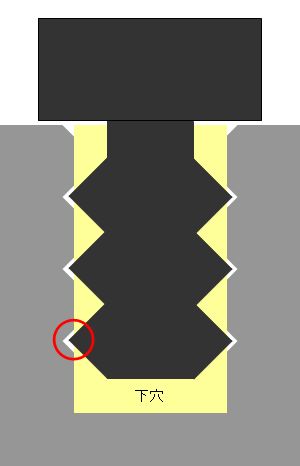
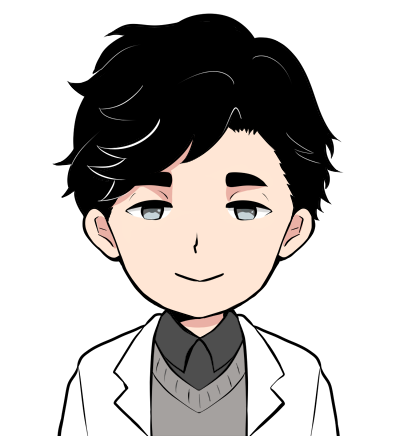
SugarBox
下穴径が大きくなると、ひっかかり率は小さくなるよ。
タップが折れにくいけど
ねじを締付けたときに、ねじ山が破壊する危険性が増すよ。
タップが折れにくいけど
ねじを締付けたときに、ねじ山が破壊する危険性が増すよ。
コメント
お世話になってます。
面取りC、Rの工具ファイルや工具データについての記事を作成して頂けないでしょうか?
他の方がインサート式でどのように登録、加工時の調整をしてるのか気になります。
コメントありがとうございます。
近日中に工具ファイル系の
記事もしくはyoutubeの動画を作成しようと考えています。
面取りC,Rの工具ファイルというワードの理解がしきれない部分があるのですが、
C付きエンドミルやR付きエンドミルに対しての工具ファイル作成なのか
面取り工具に対しての工具ファイル作成なのかが気になります。
よろしくお願いします。
言ってたのは面取り工具のR面取りとC面取りです。
エンドミルでの方も何かあるなら気になります。
宜しくお願いします。
最新記事にて少し内容を取り上げさせていただきました。
詳細な内容は中級記事として将来的に出そうかと思っていますが、
現段階の回答として十分かと思っています。
いかがでしょうか?
よろしくお願いします。
面取り工具ファイルについては最小径、最大径?呼び径?(忘れました)等の登録などを皆さんはどうしてるのかなと思ってました。ほぼカタログ値であとは削ってみて微調整でしょうか?
面取りは先端に遊びがある場合が多いため、
その部分に対応した径MINを入力しています。
おっしゃる通りで
カタログ値を参考に入力→微調整の流れです。
画像測定機等であらかじめ計算する方法などもありますが、
相当な精度なものを除き上記の方法を取っています。
ありがとうございます。
別件で質問なのですが、Φ13ハイスドリル(刃先130°ぐらいOSG-exsus、nachi-sg等)でアルミ厚み10以下に穴あけすると穴がいびつになったり切粉噛んでるのか段がついたりと安定しません。
条件等色々変えて試しましたが良い結果とは言えないものでした。一般的にハイスソリッドドリルでは13ぐらいになると厳しいもんなんでしょうか?下穴はなしです。
フラットドリルorエンドミルでとりあえずしています。
数ヶ月で前任者から引き継ぎというかたちでしだしたので一般的なこともよくわからないので教えて頂けると幸いです。
返信を新規コメントさせていただきました。
ご参考までにどうぞ!
アルミの厚み10mmというのが曲者で例えば
縦100横100厚み10mmの板だったりすると
バイスでくわえた段階でワークがしなっていると思います。
(表面をテストインジケータで走らせると膨らみが確認できる)
別サイズで縦30横30厚み10mmだったりすると
バイスでくわえてもなんともないのではと思います。
柔らかい材質なので材料サイズの影響を受けやすいです。
このしなる状態の材質に対してドリル加工をすると安定しないことが非常に多いです。
そもそもφ13は結構加工負荷が大きい方なので下穴を開けるか悩むところですね。
(φ10程度からキリ穴の場合は下穴加工が欲しいのが本音です。)
個人的にはアルミならφ11〜12.5程度のドリルでいきなり加工して
エンドミルφ10真円で高速加工にて仕上げるが一番安定して流せそうかなと思います。
フラットドリルもありですが、表面の仕上げ精度をどの程度求めているかで選択します。
(フラットドリルだと少し荒くなると思います。プログラムは楽。
キリコが絡みやすいのでは?真円の場合、キリコは絡まない)
数量や生産性でアプローチが変わってくるため、
これ!とは一概には言えませんが
このパターンだと真円加工が一番手っ取り早いことが多いです。(次点がフラットドリル)
ご参考までに。
ちなみに貫通穴を想定して真円加工をオススメさせていただいてます。
止まり穴の場合はフラットドリルの方がオススメです。
材料寸法を書いていただければ
参考プログラムを作成できるかと思います。
(対応は数日中になってしまいますが)
よろしくお願いします。
詳しくありがとございます。
厚み6〜9巾40長さ130〜140
厚み長さ違いの巾中心線上に13キリ貫通2箇所という物でした。
ちなみに厚みがある程度あればソリッドドリル一発で問題なくいけるのでしょうか?
よろしくお願いします。
>ちなみに厚みがある程度あればソリッドドリル一発で問題なくいけるのでしょうか?
これは非常に難しい問題です。
明確に答えられないというのが回答になります。
顧客がどの程度の品質を求めているかに依存するためです。
さらに加工環境等でも簡単に変わります。
個人的には回答に限りなく近い
最新記事を作成させていただきました。
長さ寸法が120だったりと違いはありますが、
よろしければ参考してください。
よろしくお願いします。